Why You Should Be Using Modbus (and IO-Link) for Predictive Maintenance
- Shane D
- Apr 14
- 4 min read
Updated: Apr 15
Why Modbus is Essential for Your Industrial Network
If you're not using Modbus in your industrial network, you're missing out on a reliable and cost-effective way to create a predictive maintenance system without overhauling your existing setup. Modbus has been a key player in industrial communication for years, making it easy to connect different devices and share data across your network.
Accessible Automation for All Sizes
Today, automation technology is available for businesses of all sizes. Advances in technology mean that even small operations can use sophisticated tools like Modbus and smart sensors like IO-Link for real-time monitoring. This helps prevent unexpected failures and optimizes maintenance schedules, leading to better efficiency and cost savings.
✅ How It Works
Sensors (vibration, temperature, flow, current) connect via Modbus RTU or TCP or IO-Link. They monitor machinery health and processes, transmitting real-time data for proactive maintenance and efficiency.
A gateway or IO-Link master collects the data and pushes it to your PLCs, HMIs, or cloud platform. It aggregates sensor data for seamless integration, enabling effective data visualization and remote monitoring.
Alerts can notify personnel via HMI screens, text/email, or create automated CMMS work orders. This ensures quick response to issues and streamlines maintenance processes.
The system can start small and scale across multiple machines, lines, or sites. This allows for a cost-effective, tailored approach to monitoring, enhancing productivity and reliability.
🔄 Why Use IO-Link Alongside Modbus?
Modbus provides robust communication over serial or Ethernet networks, but IO-Link offers enhanced device-level data and diagnostics, augmenting traditional protocols.
IO-Link in parallel with Modbus improves industrial automation efficiency:
Detailed sensor health and diagnostics: IO-Link provides real-time monitoring of sensor performance, helping identify issues before they escalate, enhancing system reliability.
Automatic device replacement: IO-Link enables automatic configuration of new devices, reducing downtime and simplifying maintenance.
Fast setup and integration: IO-Link masters connect via Modbus TCP or EtherNet/IP, streamlining integration and leveraging existing networks for quick deployment.
Modbus manages broader communication, while IO-Link provides deep sensor-level insight, enhancing predictive maintenance and optimizing operations, reducing costs, and improving equipment effectiveness.
🔧 Real-World Example #1: Sawmill Planer
A sawmill installed Modbus-based vibration sensors on a high-speed planer, crucial for shaping lumber to specific standards. Optimal performance is vital for productivity.
The sensors detected subtle vibration changes, indicating potential bearing wear. This early detection allowed for proactive maintenance. The gateway sent a fault message to the PLC, which controls the machinery.
A visual HMI alert appeared on the HMI screen, quickly informing operators of the issue. Additionally, a text to maintenance notified the team, enabling prompt intervention.
The maintenance team addressed the issue during a scheduled stop, avoiding costly unplanned downtime. This integration improved the planer's reliability and enhanced overall sawmill efficiency.
💧 Real-World Example #2: Municipal Water Pump Station
In a municipal water treatment facility, IO-Link temperature and flow sensors monitored a critical pump's performance and health in the water distribution system.
These sensors provided real-time data on temperature and flow rates. Anomalies were processed by the IO-Link master and relayed through a Modbus TCP gateway, ensuring immediate communication with the central monitoring system for further investigation.
An automated email alert was sent to the maintenance team with anomaly details, and a CMMS work order was triggered, documenting the issue for future reference.
This proactive system allowed a technician to address the issue promptly, preventing pump failure and ensuring reliable water distribution, while reducing the risk of costly repairs and service interruptions.
📊 Take It a Step Further: Visualize It All
Enhance your system with a central dashboard for a comprehensive view of operations:
Use tools like Ignition, or Node-RED to visualize live data, track KPIs, and receive alerts. These platforms offer user-friendly data display for quick assessments and informed decisions.
Dashboards can be customized by parameters like location or asset class, aiding maintenance teams and providing management visibility. Custom views support detailed analysis and a holistic overview, enhancing communication and collaboration.
Integrating data from protocols like Modbus and IO-Link provides actionable insights. This allows monitoring from asset status to sensor diagnostics, improving efficiency, reducing downtime, and enhancing predictive maintenance.
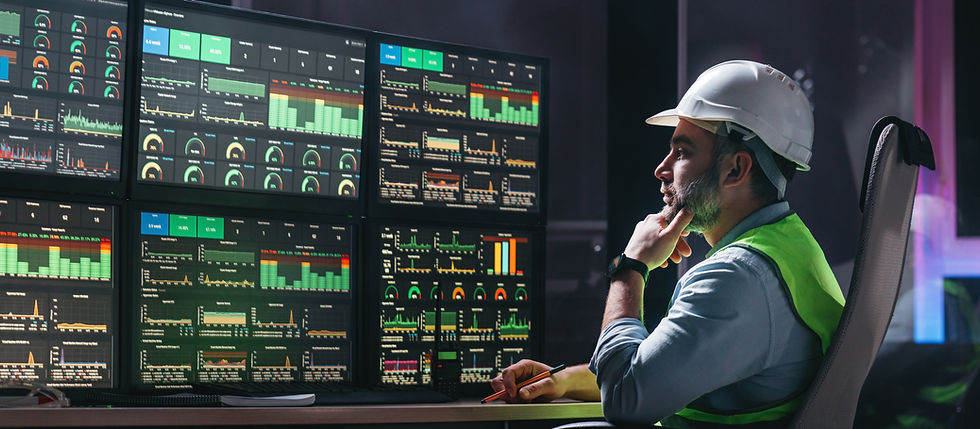
Proactive Maintenance with Data Insights
With Modbus, you can gather important data from various sensors along your production line. Analyzing this data allows you to spot potential issues before they become costly problems. Shifting to a predictive maintenance strategy helps you avoid downtime and lost revenue by addressing issues based on actual performance data.
Flexible and Scalable Solutions
The flexibility of Modbus supports different communication methods, making it easy to adapt to your facility's needs. This adaptability allows for straightforward upgrades and expansions without extensive retraining or new technology investments. Companies can scale their predictive maintenance systems as they grow, staying competitive in an automated industry.
Romulus Industrial Innovation helps manufacturers, municipalities, and industrial teams build flexible, intelligent maintenance systems that evolve with their needs.
Want help with your application? Or looking for a hybrid architecture plan? Just say the word—we can help draft a technical roadmap or tool comparison.
Comments